Lack of spare parts and costly downtime led to a technology partnership with DEIF
WEG’s previous pitch system supplier decided to exit the wind energy business, which caused WEG to experience what it considered sub-optimal delivery time, spare parts costs and customer service.
One of Brazil’s largest wind sites is situated in Sao Bento do Norte in the north-eastern part of Brazil and counts 149 of WEG’s AGW110/2.1 MW wind turbines and employs over 20 technicians. With optimum wind conditions and an annual energy production (AEP) of approximately 1475 GWh, the cost in case of downtime is enormous and must be minimised.
As a consequence of the partner’s exit from the wind industry, WEG faced difficulties to get spare parts and promptly decided to find a solution in short timeframe. “Retrofitting turbines is not something that we benefit from as we add cost to the project, but what we valued and needed the most was to keep the turbines available. As we had difficulties getting spare parts from our former supplier we decided to find a partner that could develop a cost-efficient pitch control solution in a short timeframe to keep the turbines up and running”, explains Engineer Wanderson Luiz Lupke de Oliveira who is responsible for pitch systems and design at WEG.
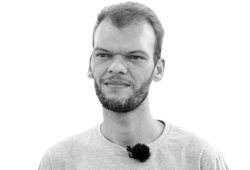
“We’re still at an early stage, but we can see an increase in turbine availability, as an effect of the new pitch system”
Wanderson Luiz Lupke de Oliveira
Engineer, WEG
The new partner was found in Denmark, thousands of kilometres from Brazil. However, the distance did not affect the partnership, and it was the beginning of close cooperation between WEG and DEIF’s engineering team. The first challenge was to design a pitch control retrofit solution that could be implemented quickly and with a minimum of changes to the existing pitch system. After completing the retrofit, the next step was to develop a complete pitch design, starting with WEG’s AGW110/2.1MW turbines. The pitch design is also going to be applied in WEG’s future AGW147/4.2 MW wind turbines.
According to Wanderson, the preliminary results are convincing, and the engineer has confidence in the solution.
“We’re still at an early stage, but we can see an increase in turbine availability, as an effect of the new pitch system”, says Wanderson.
Until now, WEG has retrofitted five turbines with the pitch control solution from DEIF but expects to retrofit the remaining turbines in the coming years.
“We have a good relationship with DEIF, and we can see that the solution is of good quality – not only the IMD drives but also the pitch controller. The controller is one of the fastest controllers on the market and uses a CODESYS basis, which is nice as you have multiple software options”, says Wanderson.
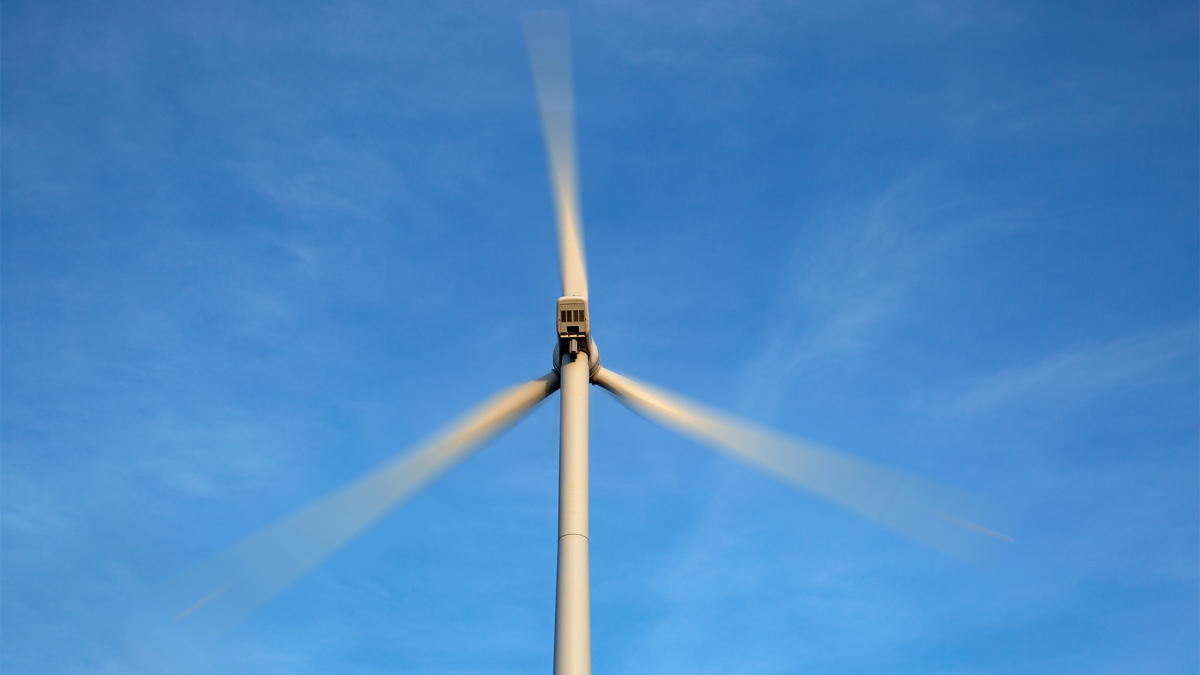
Traditional and reliable
DEIF’s solution is a traditional pitch system, but according to Wanderson, this is only an advantage in terms of spare part availability and software upgrades.
“I feel very comfortable with the solution. It is a traditional pitch system but a very reliable system. I see many modern electronic solutions with the pitch drives integrated into the cabinet, but I think the new and modern solutions on the market are very limiting. If you have any problems with the modern solutions or need spare parts, you only have one supplier to go to, and it can warp the pricing,” explains Wanderson.
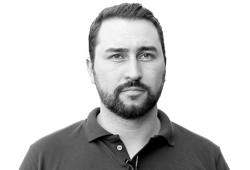
"The interfaces are easy to work with, and we can address alarms quickly which reduces the turbine shutdown time for the turbines, having the system installed"
Marcelo Bitencourt
Lead Technician, WEG
WEG’s engineering team has visited DEIF’s headquarters in Denmark to get to know the system, and also the service technicians onsite in Brazil have been trained in using the system. The training was conducted by DEIF’s Application Software Engineer Christian Reichmann, and the participants were very enthusiastic and dedicated.
The on-site service team has been working with the new system for a while, and the first experiences are positive. The service technicians find the system intuitive, and they can react faster and thereby reduce downtime.
“The interfaces are easy to work with, and we can address alarms quickly which reduces the turbine shutdown time for the turbines, having the system installed”, explains Lead Technician Marcelo Bitencourt.
Beneficial side-effects
Besides increasing turbine availability and being more user-friendly, WEG also has discovered another positive effect from the retrofit solution in terms of blade calibration.
“One of the advantages we have noticed is concerning the calibration of the blades. It is a lot easier to calibrate both the encoder and the resolver using the new software, which is totally interactive and user-friendly. It offers a range of possibilities that allow us to be more precise when making the settings”, explains Technician Jhonatan Dias.
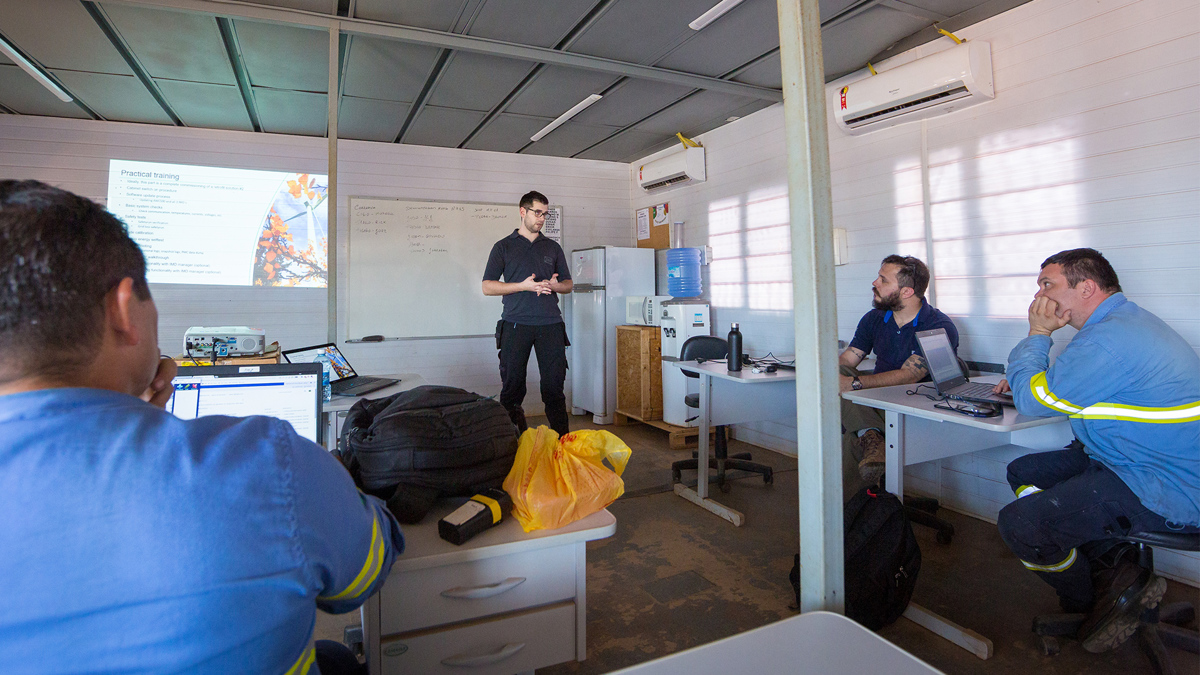

"One of the advantages we have noticed is concerning the calibration of the blades. It is a lot easier to calibrate both the encoder and the resolver using the new software, which is totally interactive and user-friendly. It offers a range of possibilities that allow us to be more precise when making the settings"
Jhonatan Dias
Technician, WEG
Fast replacement and minimum changes required
Choosing DEIF’s pitch solution meant only a minimum of modifications to the turbine, making the retrofit cost-effective, quick and easy.
“With DEIF’s solution, we can keep the same controller interface and most key components like cables, motors, cabinets, ultracapacitors, support beams, so it was more or less just plug’n’play. We only had to replace the drives and the main controller and make some minor software adjustments. With the solution from DEIF, we now have more features, and it is easier to see the alarms and follow the turbine status,” Wanderson explains.
A point of view that is shared with the service team working onsite. Technician Jhonatan Dias was part of commissioning the retrofit, and he explains “We find the system and all the components easy to handle – both the software, the electrical and mechanical parts and it becomes even easier to commission and operate the system every time”, he concludes.
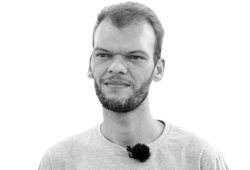
"With DEIF’s solution, we can keep the same controller interface and most key components like cables, motors, cabinets, ultracapacitors, support beams, so it was more or less just plug’n’play. We only had to replace the drives and the main controller and make some minor software adjustments. With the solution from DEIF, we now have more features, and it is easier to see the alarms and follow the turbine status"
Wanderson Luiz Lupke de Oliveira
Engineer, WEG
New wind farms with 43 WEG 4.2 MW turbines in 2022
The relation between WEG and DEIF has developed from being a supplier-customer relation to DEIF being a technology partner for WEG, designing a pitch control solution for WEG’s upcoming 4.2 MW turbine that WEG will install and commission by the end of 2022.
“Right now, we’re developing the AGW 4.2 MW turbines that also includes DEIF’s pitch control system and the prototype will be running until the end of 2020,” Wanderson explains.
WEG has signed an agreement to supply 43 AGW 147/4.2 MW wind turbines to new wind farms for Aliança Energia, and the project is expected to be completed by the end of 2022.
-
Contact us to discuss your options
- 90 years of energy pioneering
- Manufactured at the highest standards
- Superior quality
- Unmatched service and support
- Made in Denmark